Introduction to IoT in Industry 4.0
IoT in Industry 4.0, IoT will make a huge impact in the industrial sector it will make the industrial process really quick and safe. Internet of Things means connecting several device by using several software and other technology. Every one of us has come across or heard about Industry 4.0 in one way or the other. By definition, an industry is concerned with the economic activities of the production or processing of raw materials or the production or manufacturing of goods and services in a factory.
Improving production by the use of IoT Analytics in Industry 4.0 has been the talk of the town. One of the prime concerns of any industry, amongst many others, is regarding production efficiency – the higher the efficiency, the better for the company.
In order to successfully run an industry, the management needs to thoroughly analyze and address the following questions:
- What to produce?
- How to produce?
- When to produce?
- How long it takes to produce?
With the increase in complexity of the product along with the product life cycle and the demand for a certain product with respect to the others to name a few, factories face numerous challenges. As a result, they are increasingly relying on advancements in technologies to solve these limitations. Currently, what the manufacturers are leveraging on is the Industry 4.0 trend, which comprises of smart technologies like the Internet of Things (IoT), specifically the Industrial Internet of Things (IIoT), Artificial Intelligence, Machine Learning, Robotic Process Automation, etc. to name a few. Evidently, IoT has become one of the foundational measures adopted that is driving towards smart production.

With the implementation of sensors, manufacturing processes have simply stepped up. Sensors are beneficial in providing real-time information regarding the assets – namely the machines and the products, production lines, and processes. However, sensors can be relied on only for the purpose of sensing a specific change in the field variables and transferring this data to the control devices.
The real benefit is achieved when this collected data is analysed by the manufacturers to derive meaningful insights regarding the process. Interestingly, over the years, many manufacturers have been turning towards decisions based on IoT analytics to derive the most benefits from their business models.
Before we dive into the subject of IoT analytics, it is essential that we discuss the concept of Digital Twin. It is nothing, but a dynamic and virtual representation of physical devices which is used to perform simulations before the actual devices are built and deployed. The Digital Twin is created to receive the data collected by sensors from real-world situations.
Through this simulation of the physical object in real time, valuable insights on performance and potential problems of the process are obtained. The Digital Twin concept is changing the way how technologies such as Artificial Intelligence (AI), IoT, and Data Analytics are being optimized.
IoT Analytics
The data collected from sensors need to be contextualized and noise-free as these will create a large impact on the operational efficiency of any device. The real-time analysis of sensor data also termed in-stream analysis, is carried out via frameworks like rules. Through this approach, the identification of critical events and the adoption of appropriate actions becomes optimized. For instance, imagine that a sensor monitoring a particular piece of equipment detects that it is overheating while in operation.
If a rule is set up to notify the operator or to take another necessary control action once the temperature crosses a threshold limit, an unfavorable situation can be averted. This aids in ensuring the smooth and efficient running of the equipment without having the operator perform regular safety checks. Additionally, analyzing the sensor data would provide insights into what caused the particular problem and the necessary rectification can be undertaken.
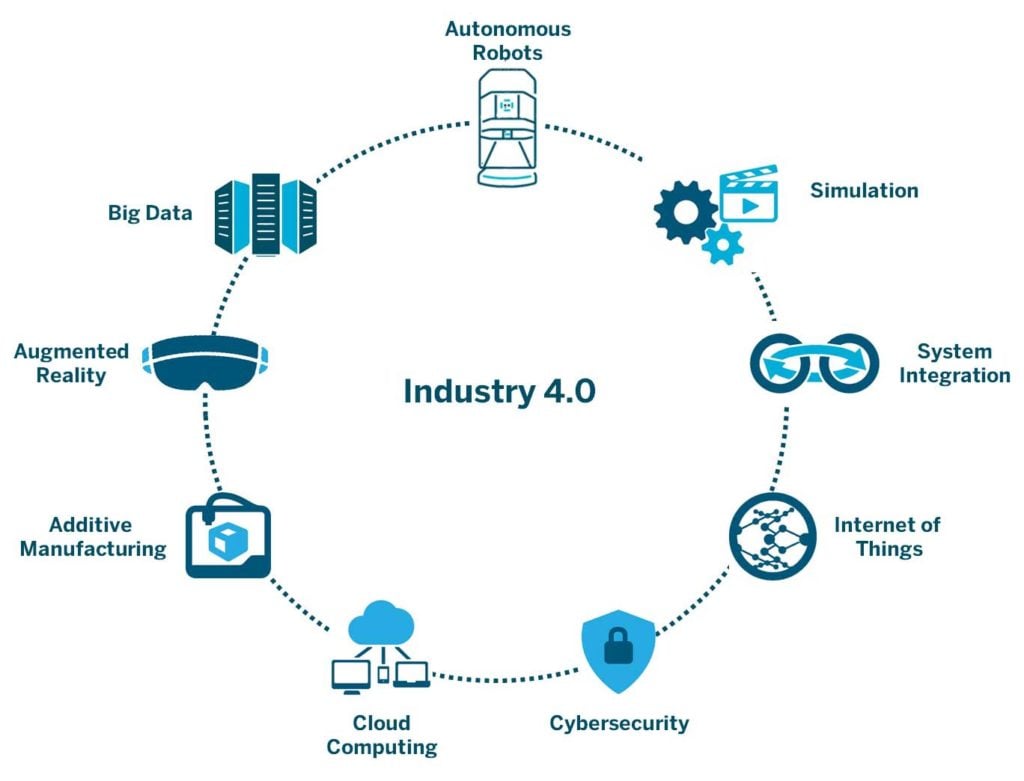
With the implementation of Industry 4.0, supply chain practices are becoming more responsive and adapting to the quickly changing external situation. Manufacturers are gaining better insights based on the telemetry collected from the assets. Artificial Intelligence is also being utilized to come up with predictive models and thereby add intelligence to the machines. The results obtained from the predictive model analysis is then utilized in predictive analytics, thereby enabling manufacturers to undertake preventive maintenance as opposed to run-for-failure maintenance.
Today, with the increasing competition due to globalization, manufacturers are heavily relying on technology to survive in the race. No one wants to be left behind. Through the latest technological advancements, it has become effortless for manufacturers to analyze the operational parameters of the machines and plan for future production through digital and resilient supply chains.
Best IoT Course Training Center in India?
SMEClabs provides high-end training in various courses for IoT and IIoT. On IoT courses starting from basic level embedded system courses and low-level programming. IIoT courses start from the basics of electrical and automation courses.
Impact of IoT in communication?
Embedded systems and VLSI use communication via IoT